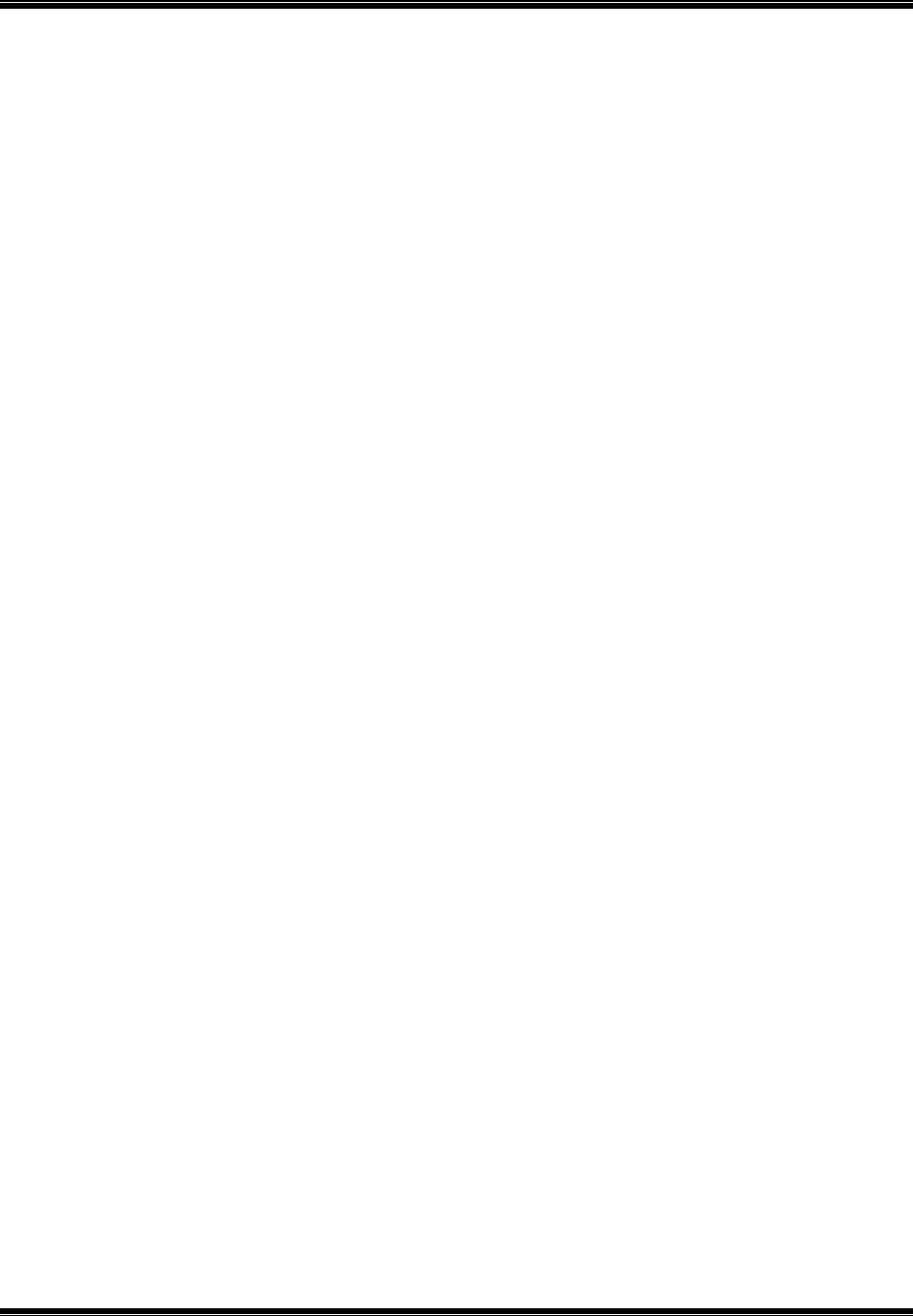
PNEUMATIC STAMPING MACHINE
Department of mechanical engineering-ATME mysore Page45
References
[1] P.M.Pradhan, “Experimental Investigation and Fabrication of Pneumatic Punch”,
International Journal ofInnovative Research in Science, Engineering and Technology, Vol. 2,
Issue 6, June 2013.
[2] A.S. AdityaPolapragada& K. Sri Varsha, “Pneumatic Auto Feed Punching and Riveting
Machine “, International Journal of Engineering Research & Technology (IJERT) Vol. 1 Issue 7,
September - 2012 ISSN: 2278-0181.
[3] U.P. Singh, “Design Study of the Geometry of a Punching tool”, Journal of Materials
Processing Technology, 33 (1992) 331-345 Elsevier.
[4] P.C.Sharma, “Methods of reducing Cutting Forces”, Pages 63-66, Production Engineering,
Ninth edition, 2004, S. Chand & Company Ltd.
[5] E. Paul. Degarmo, “Shearing in Metal Cutting”, Pages 518-528, Materials and Processes in
Manufacturing, Eighth edition, 2003, Prentice Hall of India Pvt Ltd.
[6]P.Goyal, “Review on Pneumatic Punching Machine and Modification in Punch Tool to
Reduce Punching Force Requirement”, ISSN 2394 – 3386, Volume 2, Issue 2, February 2015
[7]A.S. AdityaPolapragada et al, “Pneumatic Auto Feed Punching and Riveting Machine”, Vol.
1 Issue 7, September - 2012
[8] GauravPradipSonawane, “Design, Analysis and Manufacturing of Hydro-pneumatic Press
Machine”, Vol, 04 || Issue, 11 || November– 2014
[9]ArunS et al, “Automatic Punching Machine: A Low Cost Approach”, Volume 4, Number 5
(2014).
[10] K. Mahadevan, Design Data Handbook, Third edition, Reprint 2002, CBS Publishers &
distributors.